Microscope low-cost motorized stage
Create a precise motorized stage for an inverted fluorescence microscope for under $100 so that more precise and efficient measurements can be done, while making it accessible to those with inadequate funding to purchase expensive alternatives.
Project Overview
The two inverted fluorescent microscopes in the teaching lab of the Engineering Centers Building utilize stages that must be manually moved with two adjustable knobs. This method of adjusting the stage is not precise and does not allow for automated imaging of coordinate based locations. The current adjustment system also does not allow for a reference of the distance traveled which further decreases the precision of the instrument. Solutions for this problem do exist, however, they are costly. Kits and instructions to fix this problem go only as low as approximately $300 dollars. Microscopes with built in motorized adjustment systems can be as expensive as $70,000 new and $19,000 used. To increase the availability and widespread use of this type of solution, we aim to build ours for under $100. Our goal is to improve upon the previous designs, maintain accuracy of the instrument throughout the testing process, and to have a movement resolution of one micrometer (1µm).
Team Picture
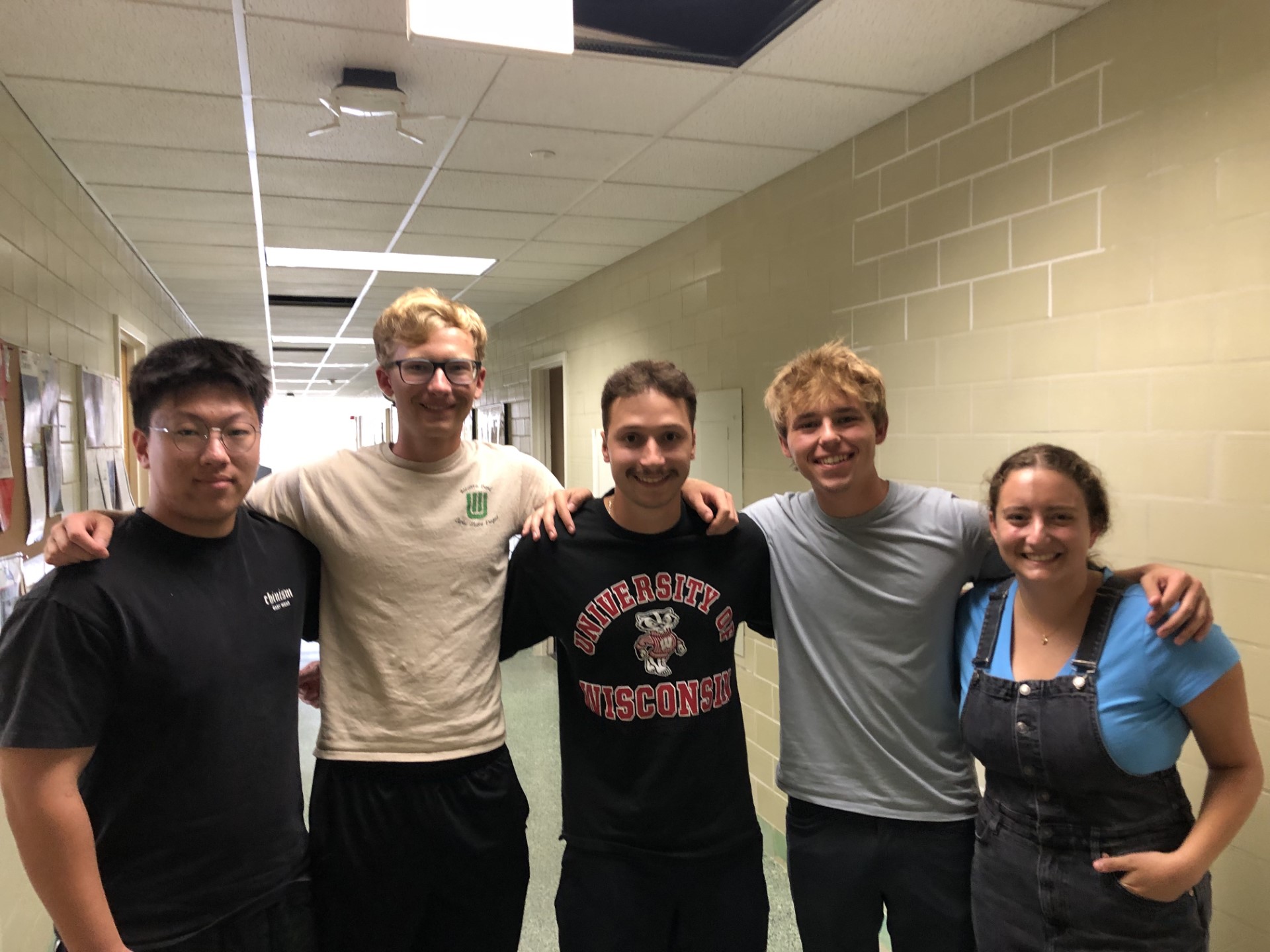
Images
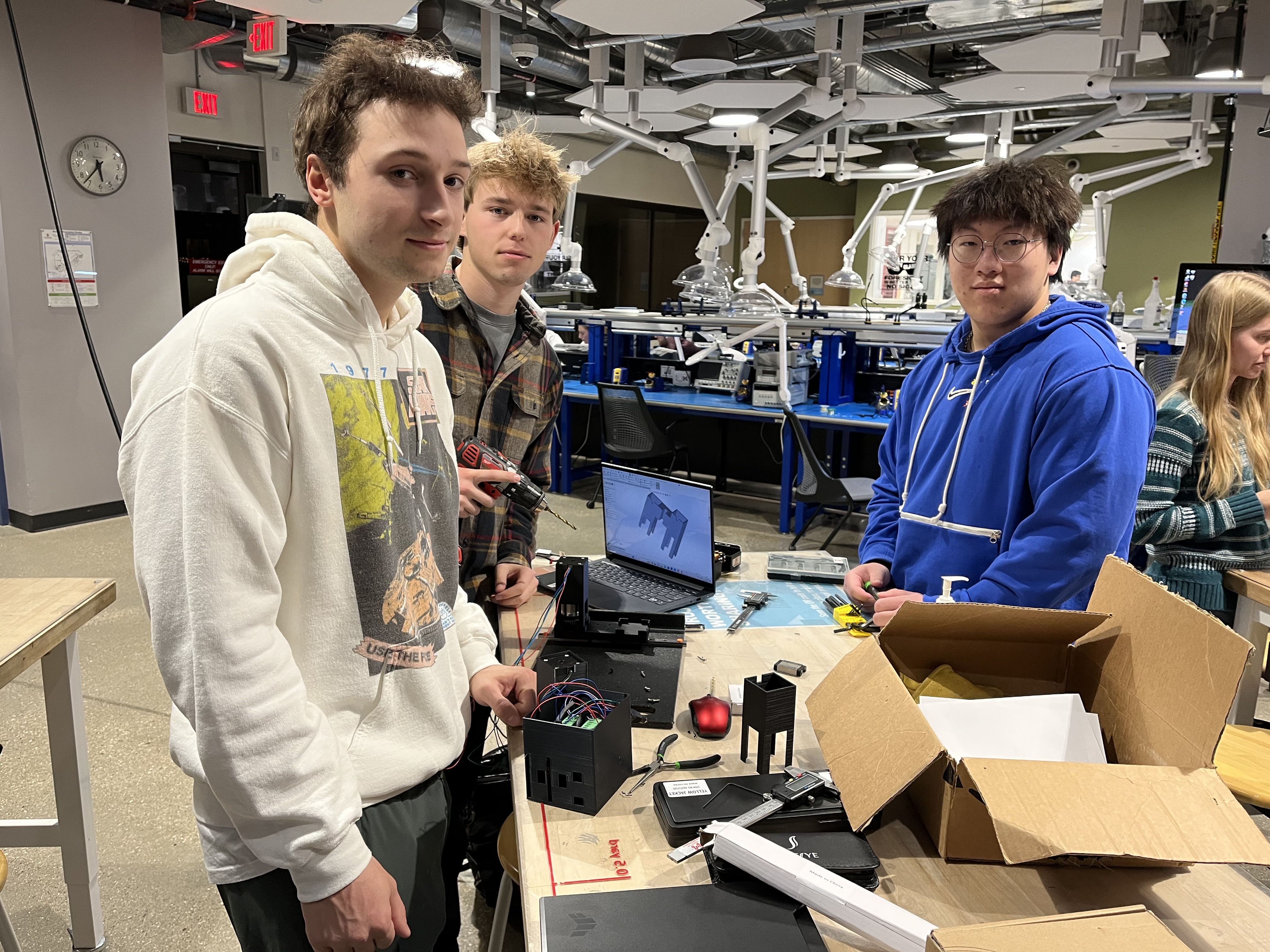
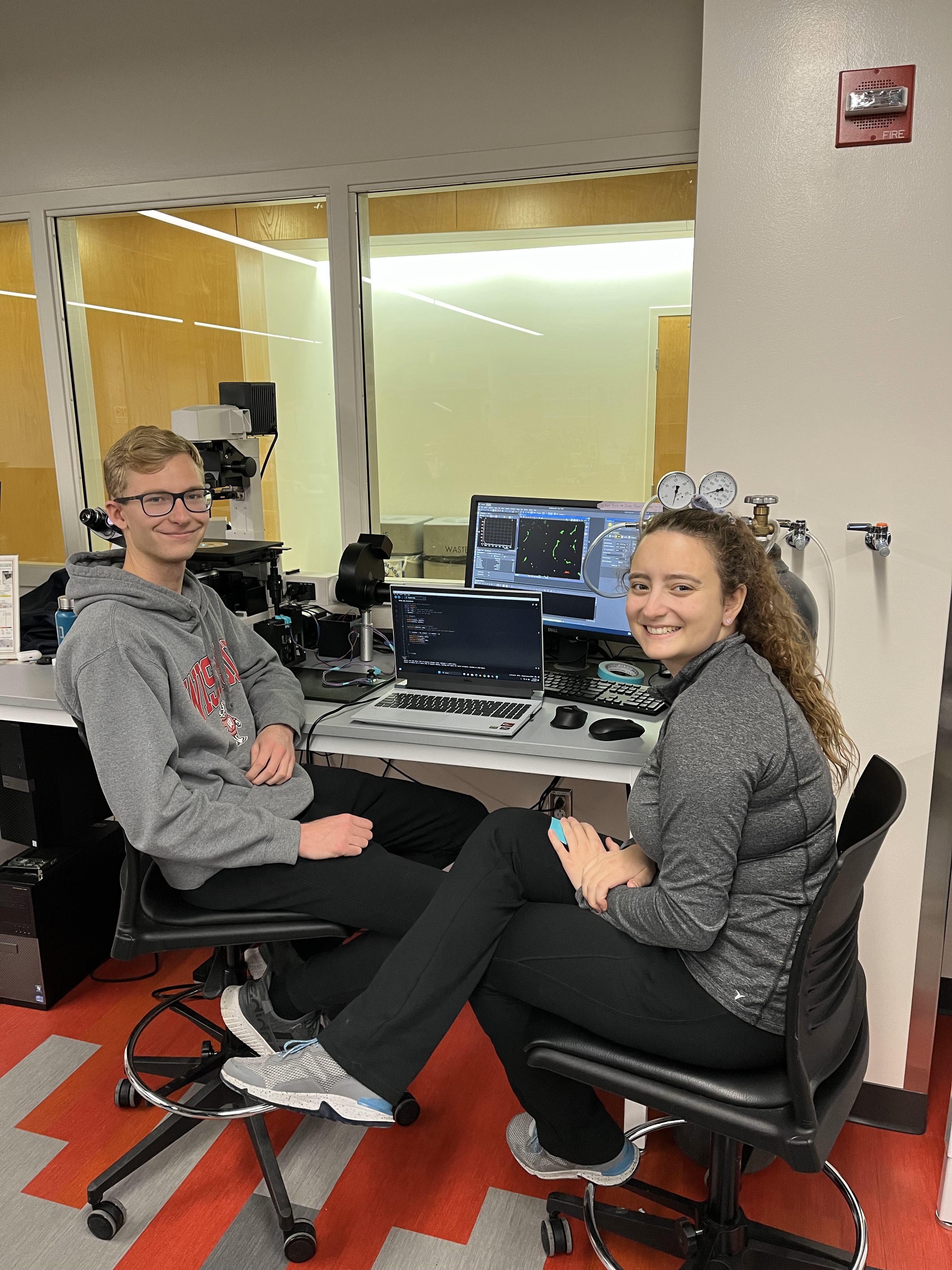
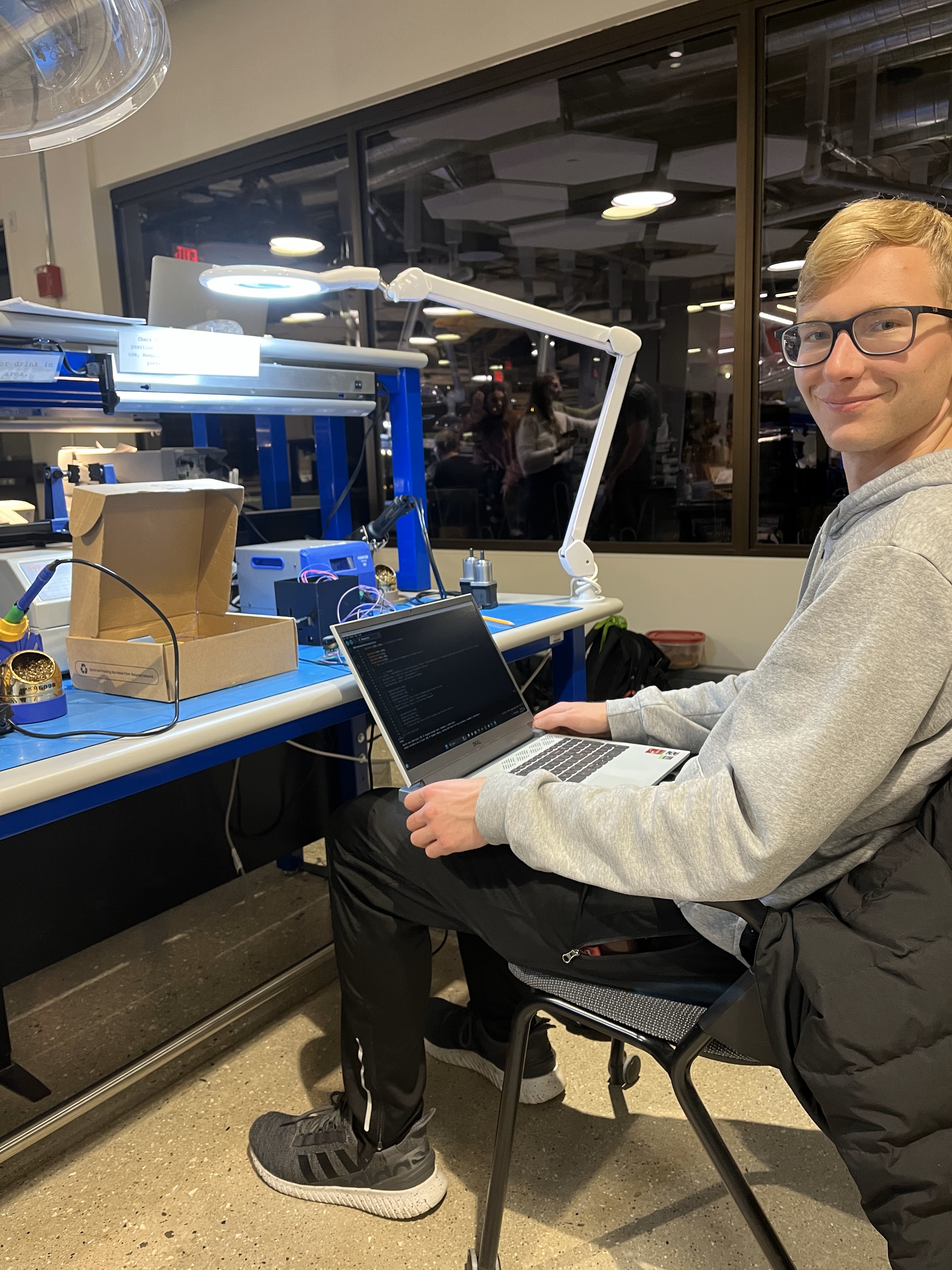
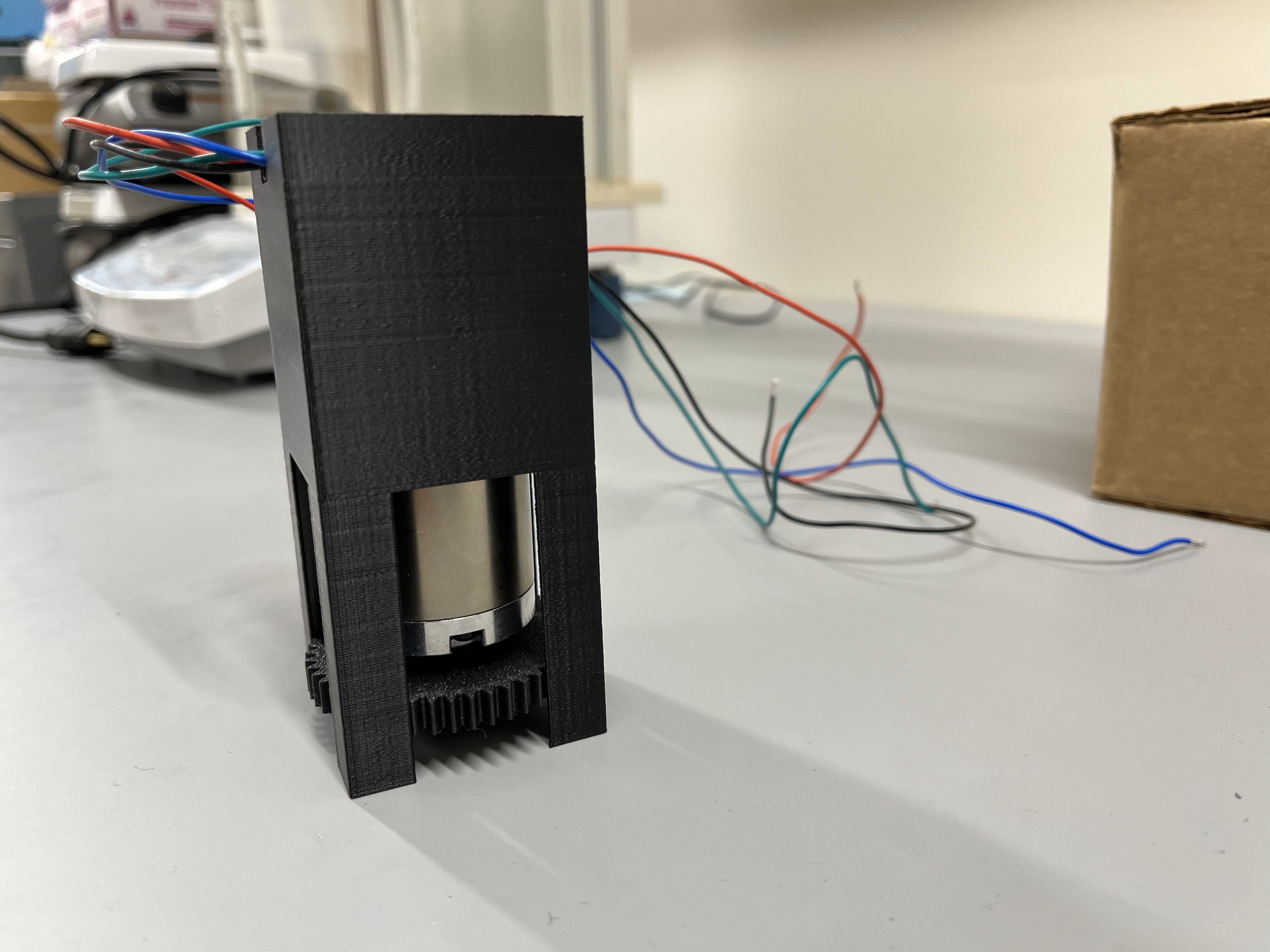
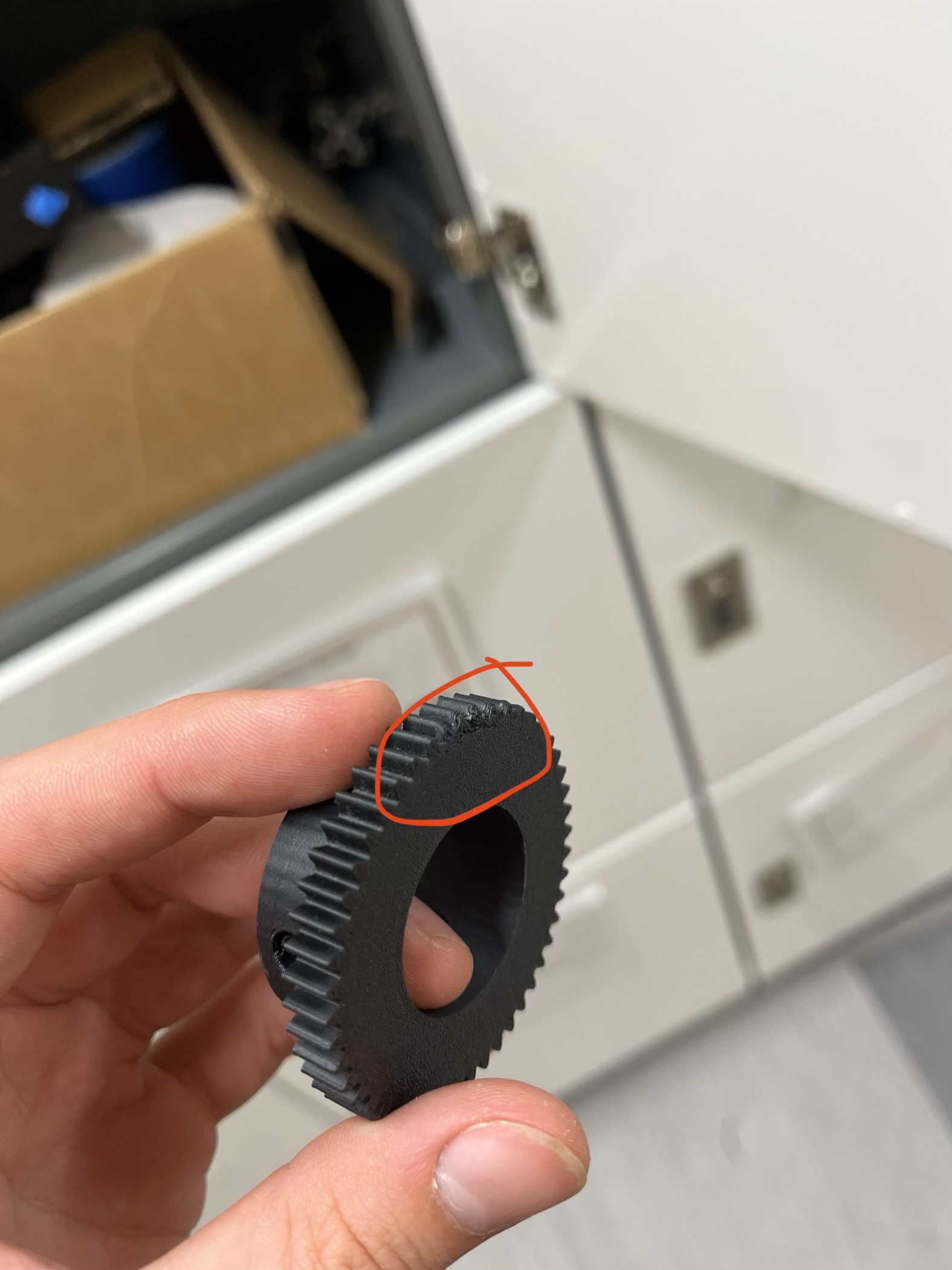
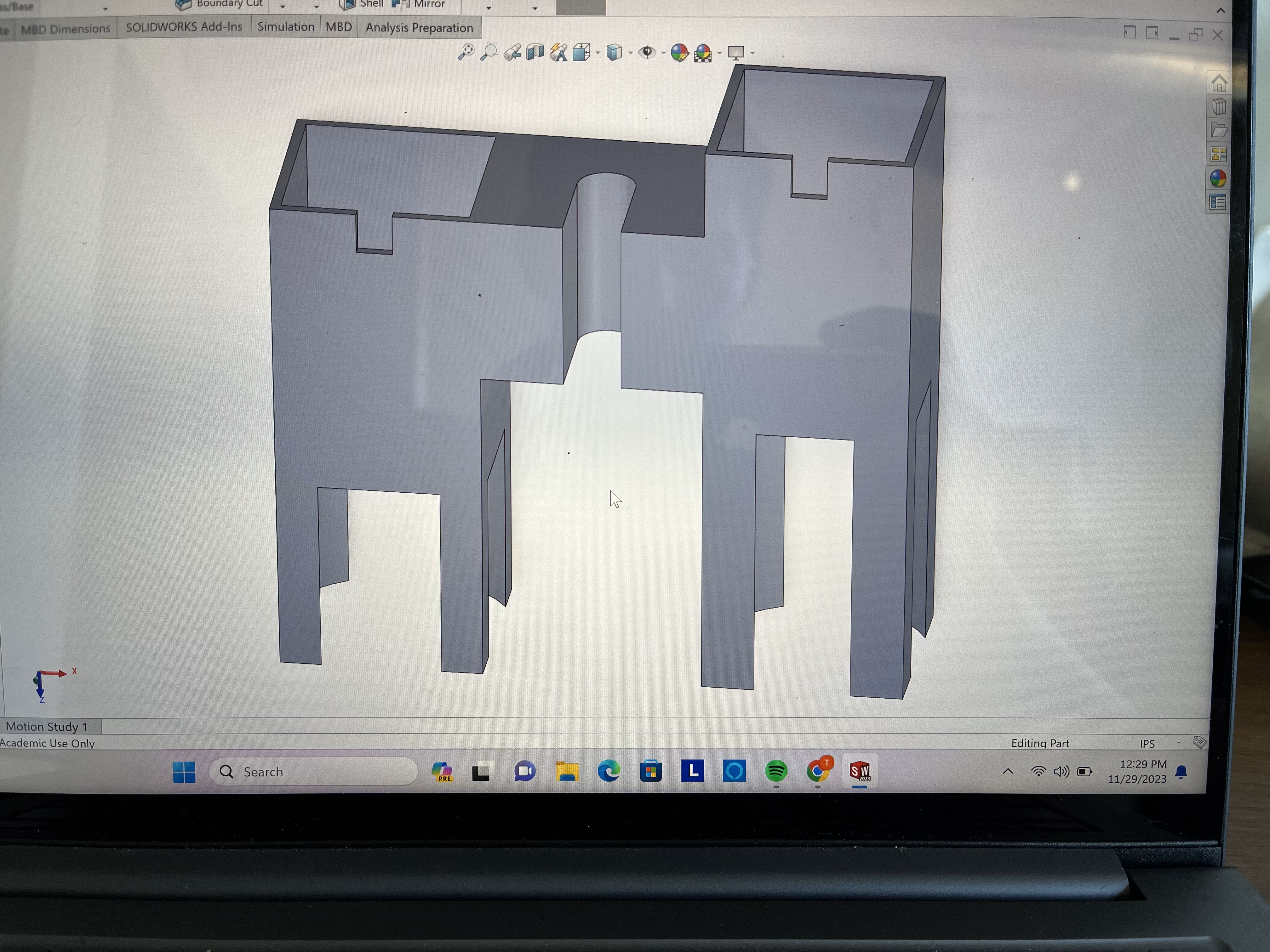
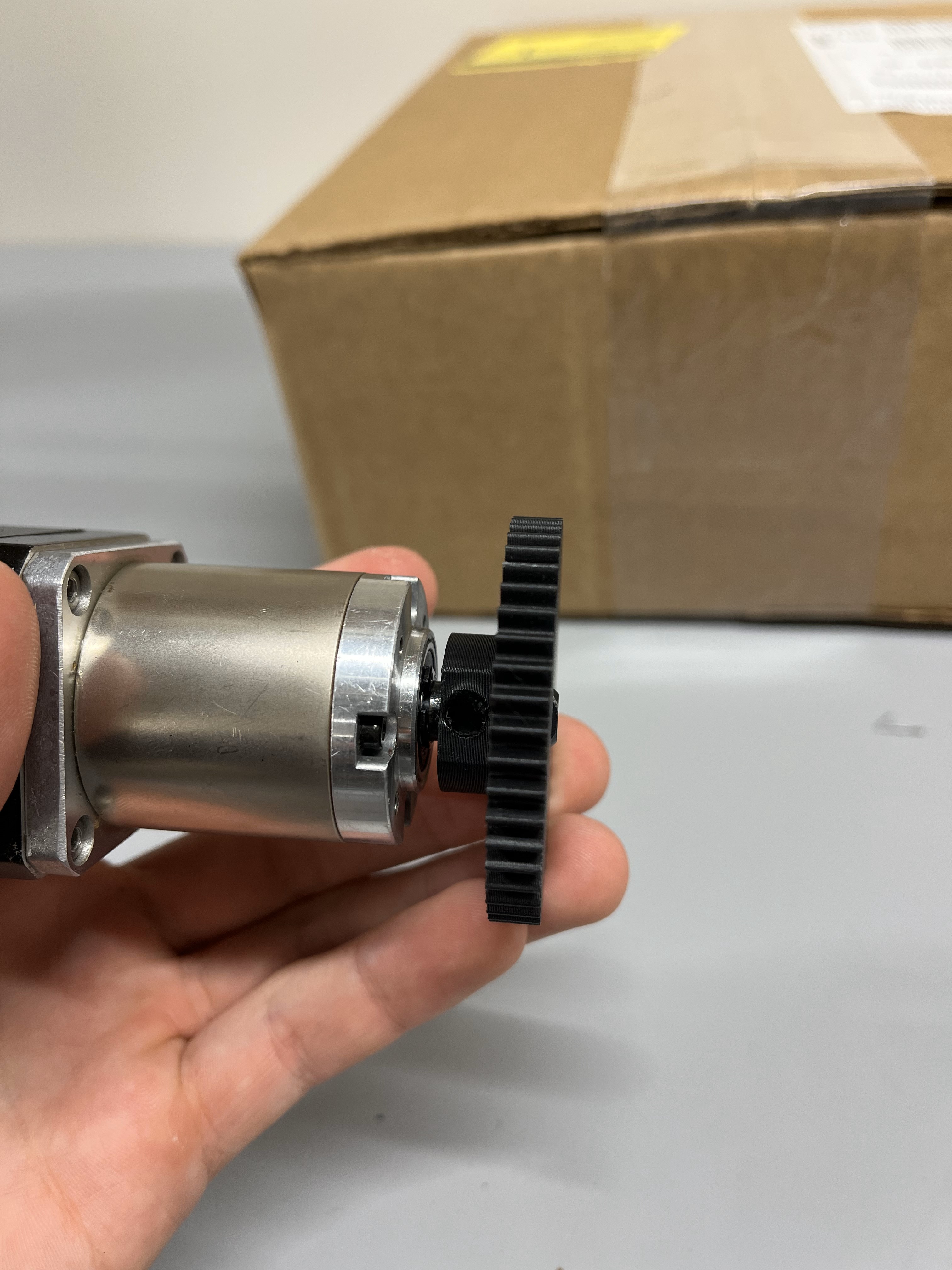
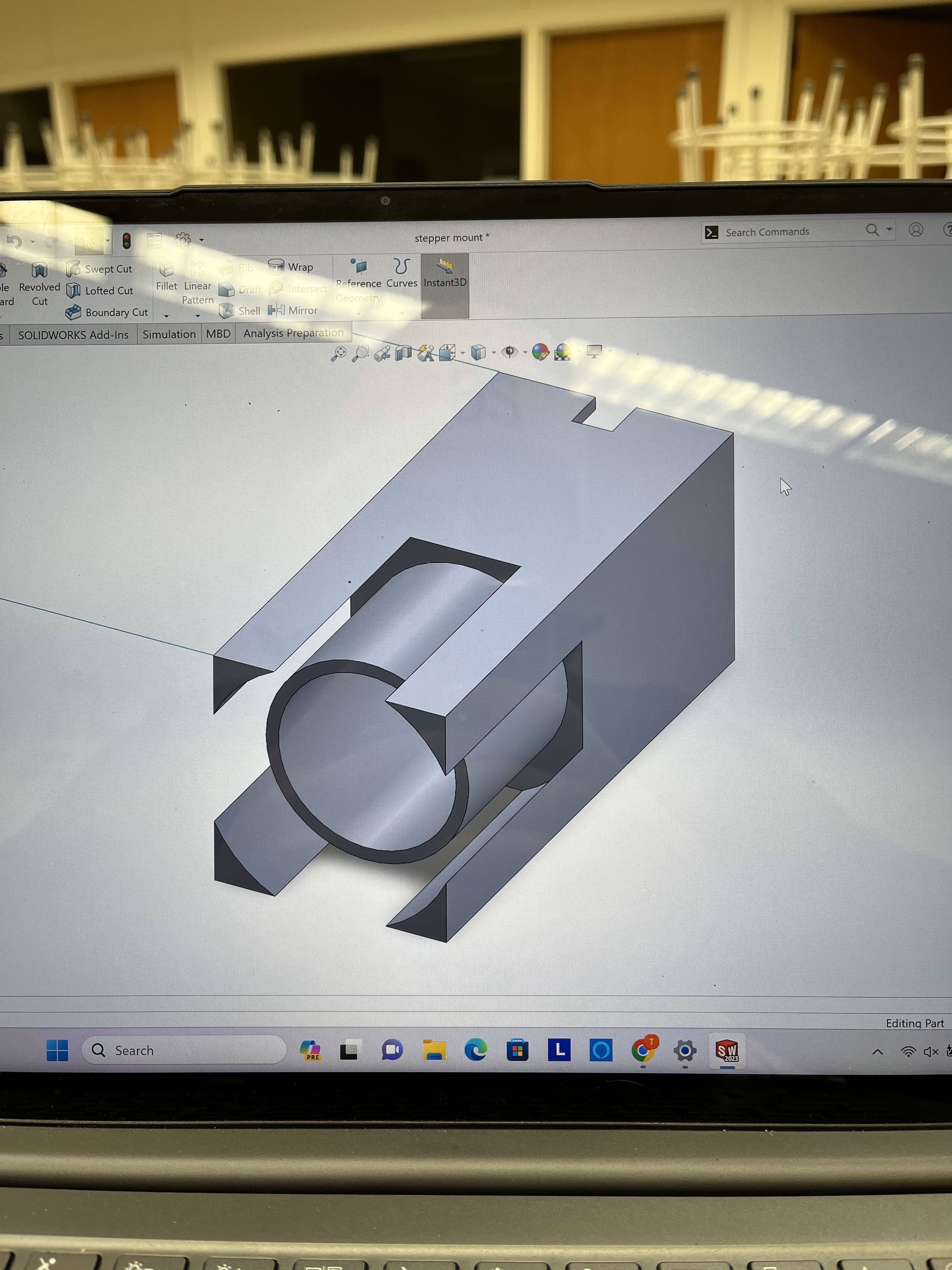
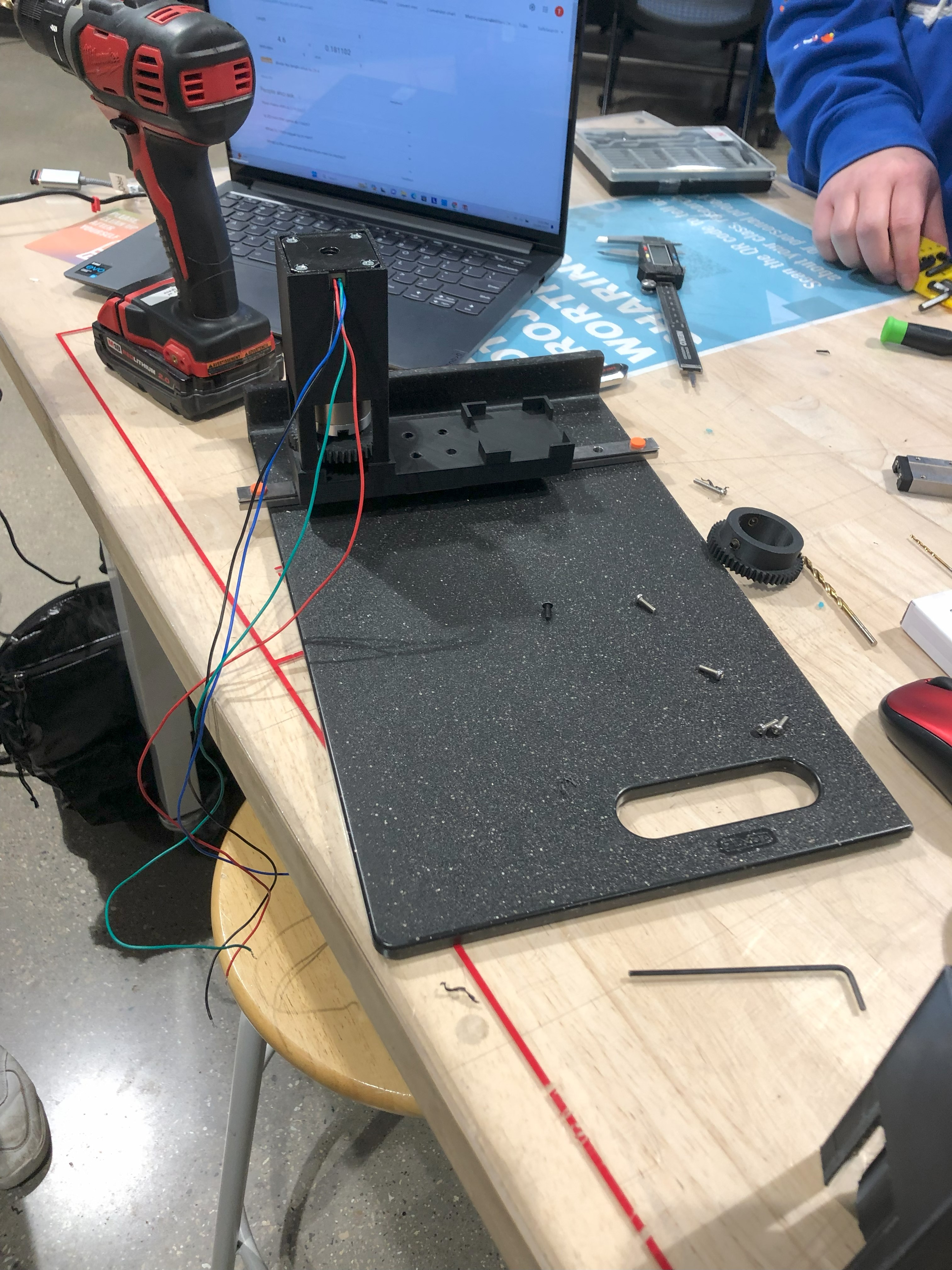
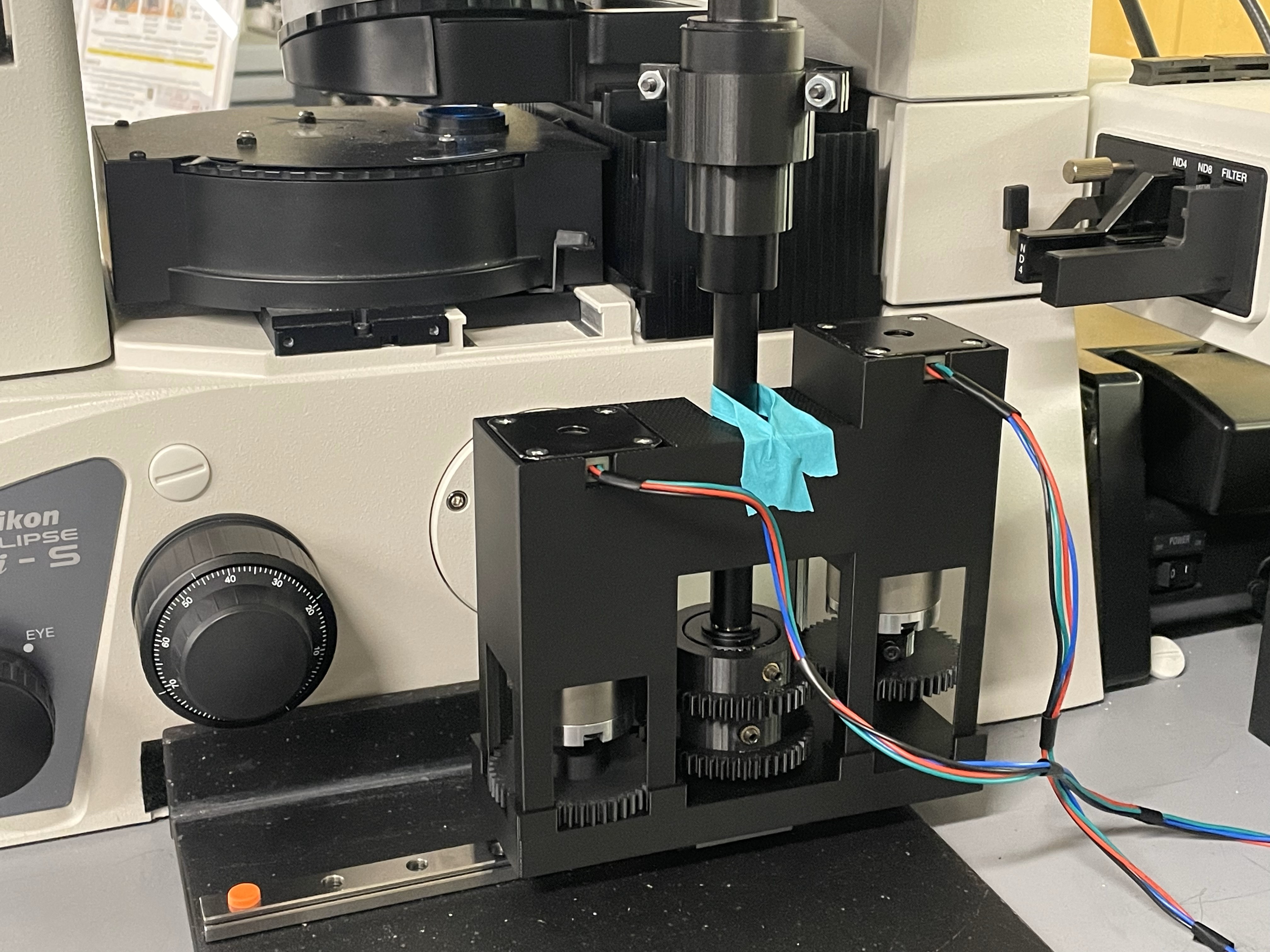
Files
- Final Notebook (December 15, 2023)
- Final Report (December 15, 2023)
- Final Poster Presentation (December 7, 2023)
- Preliminary Presentation (November 9, 2023)
- Preliminary Report (October 13, 2023)
- PDS (September 22, 2023)
Contact Information
Team Members
- Tyler Haupert - Team Leader
- Nicholas Symons - Communicator
- Julia Salita - BSAC
- Sawyer Bussey - BWIG
- Zhaoyun Tang - BPAG
Advisor and Client
- Prof. Joshua Brockman - Advisor
- Prof. John Puccinelli - Client